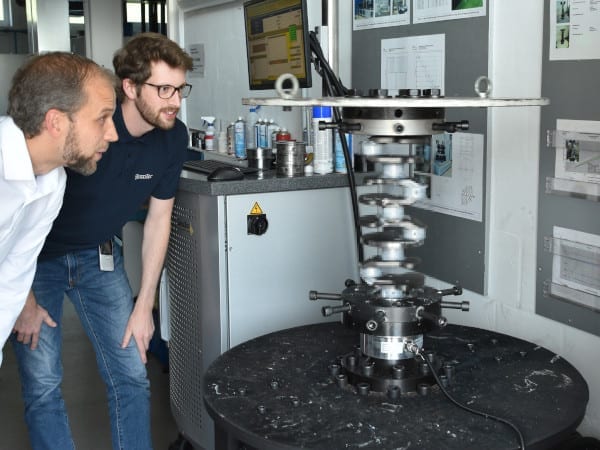
Fatigue tests according to
DIN 50100, ASTM E466-15, and ISO 1099
The fatigue test evaluates components or materials’ capacity to endure stress. Depending on whether samples are tested in their domain of infinite or finite fatigue life, experimental results are determined either by constant amplitude, block program, or increasing load-step tests.
The results of norm-based dynamic fatigue testing allow us to determine a Woehler line, an S-N curve, and/or the average infinite fatigue life of components and materials.
Our Services
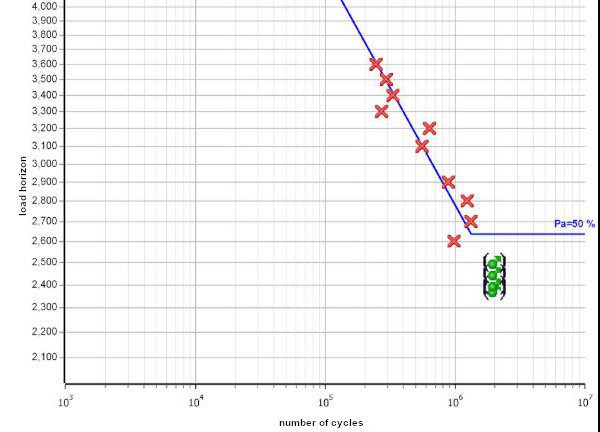
Fast results
Use resonance test technology to determine a Woehler line in 14 days
With average test frequencies between 30-150 Hz and frequencies up to 1,100 Hz possible, the diversity of test rigs in our laboratory means we have the optimal high-frequency resonance test rig for your sample.
Through individual consultations, we can adapt the fatigue test to perfectly suit your components.
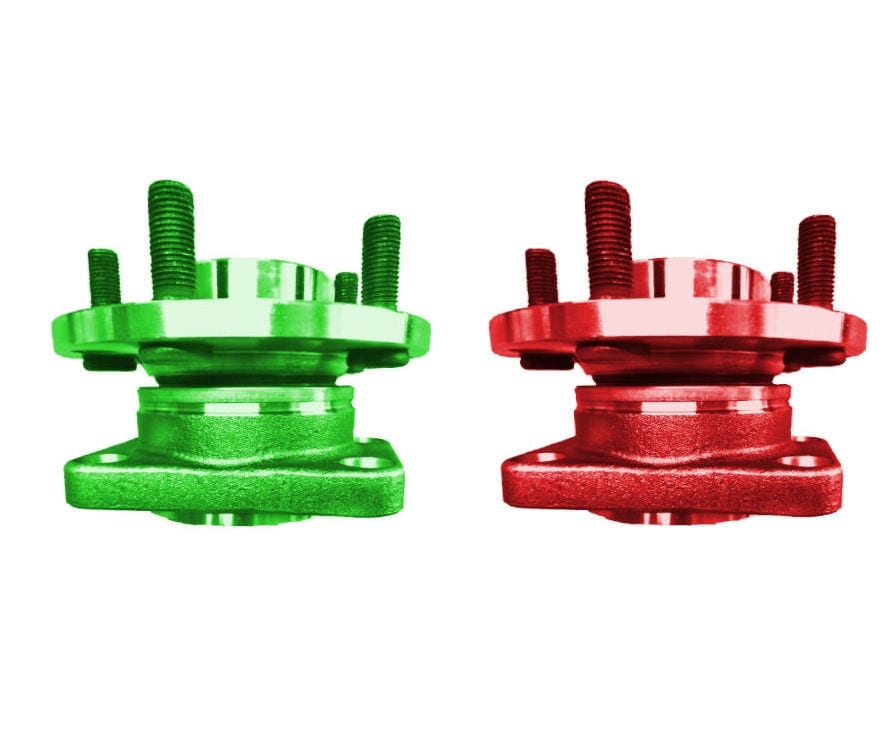
A/B Variant Comparison Testing
Do updated components perform similarly or better?
Small changes in geometry, alloy, or surface can have significant impacts on a component’s dynamic strength.
A/B comparison testing allows you to compare the lifetime of promising new iterations of a part with that of its predecessors.
Supplier quality
How do new and old suppliers compare?
Changing part suppliers carries certain risks. Will the manufacturing quality be lower? Is there a high variance in quality among parts from one supplier? What is the tensile strength of the material composition?
Our results are determined as a Woehler line, allowing you to compare your components and suppliers.
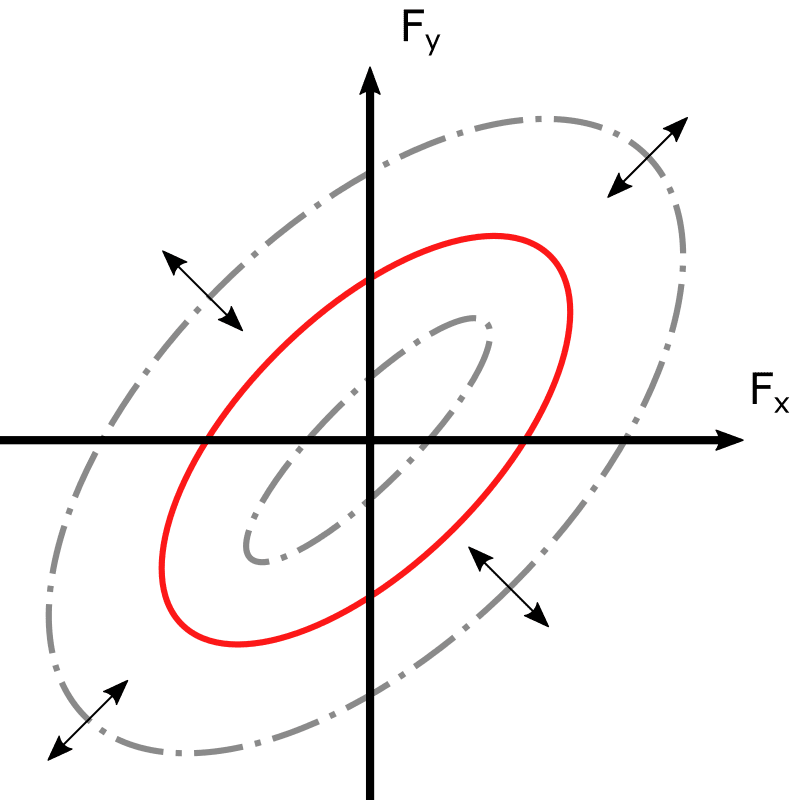
Multiaxial resonance tests
The best of both worlds
Multiaxial testing can also be conducted when single-dimensional loads do not accurately replicate the operational loads a component experiences.
The targeted overlay of two dynamic fatigue rigs generates multiaxial load cases on a component, with all of the advantages of resonance testing: speed, cost-efficiency, and crack detection.
Overlays:
- Torsion + bending
- Torsion + radial load
- Tension/compression + tension/compression
- etc.
Typical components:
- Crankshafts, camshafts
- Differential baskets
- Cylinder crankcase
- All types of rolling bearings, transducers, flexplates, and transmission and propulsion components for trains
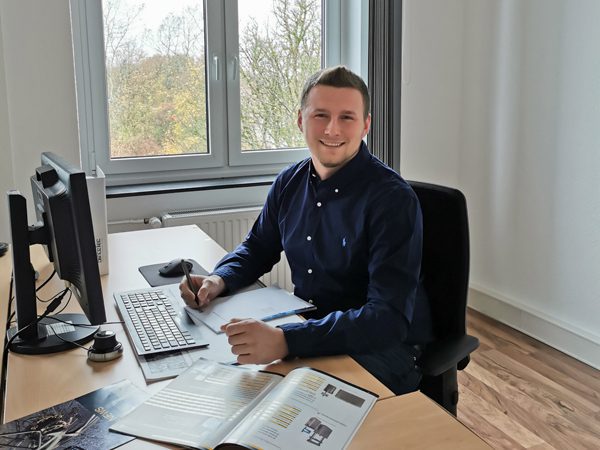
Contact Us
We have testing solutions for all manner of components, assemblies, and materials to determine their maximum load capacity, lifetime, and reliability. Contact us below with a summary of your testing needs and we will reach out to you as soon as possible.
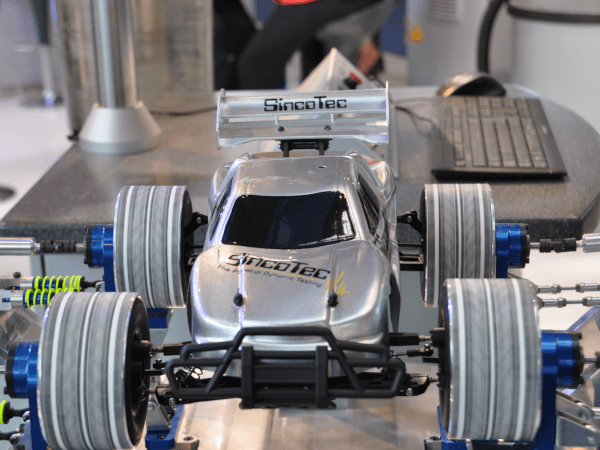
Specialized Testing
We can test anything
Apart from our standard test protocols, we use SincoTec’s toolbox of proven modular test elements to collaborate on the development of new testing methods and protocols. From changing the drive system to simulating specific environmental conditions, our aim is to make the impossible, possible. Always on the cutting edge, we have used this methodology to develop many new testing protocols and standards.
- Multiaxial test loads
- e. g. combining torsion and bending loads or a shaker test with simultaneous pulsating internal pressure
- Collaborative development
- Highly realistic operating-load simulations in our test laboratory
DIN
Norms
Testing to customer or general norms
- DIN 50100
“dynamic fatigue test – implementation and evaluation of cyclic tests with constant load amplitudes for metallic material samples and components” - ASTM E466-15
„Standard Practice for Conducting Force Controlled Constant Amplitude Axial Fatigue Tests of Metallic Materials“ - ISO 1099
“metallic materials – fatigue tests – axial strength-regulated - DIN EN 6072
“aeronautics and space – metallic materials – test methods – fatigue test with constant amplitude”