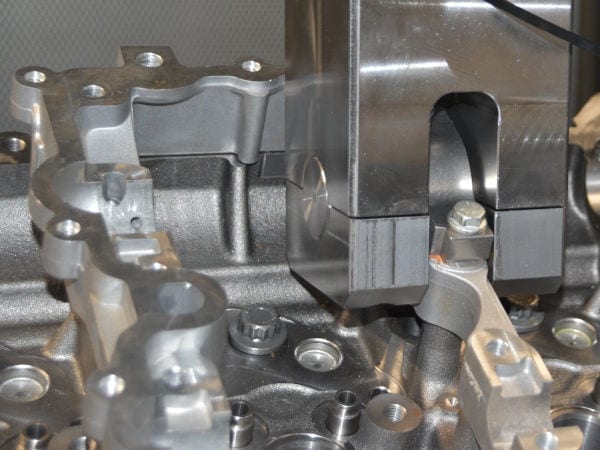
Our component-specific test systems
Testing machine for motor components
These test systems for motor components are designed to test the fatigue strength of components experiencing high torsional loads or free torsional oscillation, bending and torsional stresses, and/or combinations of the above. Parts that experience such loads in real life include crankshafts, electronic motors, and generator shafts.
Quick navigation:
POWER TORQUE
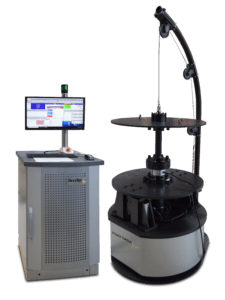

Torsion
Torsional fatigue test system for crank, drive, and camshafts as well as wheels and material samples
- 6 test rig sizes at nominal loads between 500 Nm and 40,000 Nm
- High test frequencies up to 110 Hz
- Very low energy consumption <1 kWh
- All advantages of resonance testing technology
Typical Components:
- Electric vehicle motors
- Flywheel
- Gearbox components
- Flange joints
- Crankshafts
- Camshafts
- Driveshafts
- Metallic and fiber-reinforced synthetic materials material samples
POWER BENDING
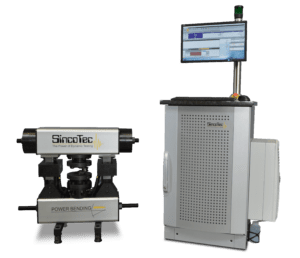

Bending
Bending test system for crankshafts, shafts, and material samples for personal and commercial vehicles and shipping
- 8 test rig sizes at nominal loads between 1,000 Nm and 30,000 Nm
- 4-point bending (the bending moment is constant across the entire test sample)
- Test frequencies can be influenced in gradations
- Very low energy consumption <1 kWh
- All advantages of resonance test technology
Typical Components:
- Crankshaft segments
- Shafts
- Flywheels
- Metal and fiber reinforced synthetic plastics material samples
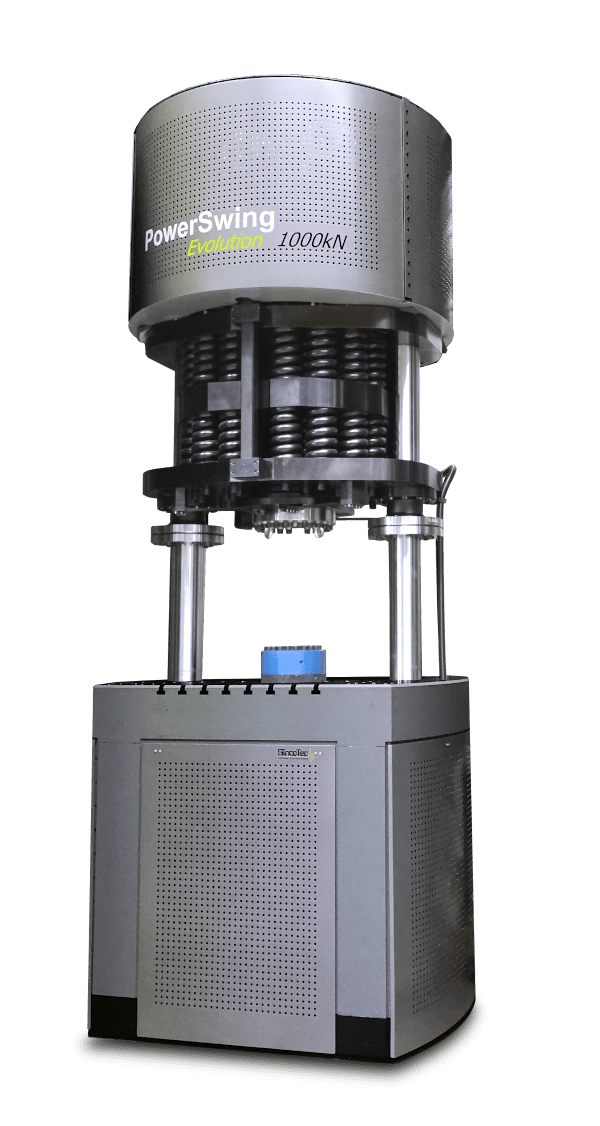
Dynamic test rig for fatigue testing
POWER SWING MOT
Our universal testing machine POWER SWING MOT can be used to conduct fast, precise, and energy-efficient fatigue testing on motor components such as:
- Connecting rods
- Gearboxes
- Rocker arms
- Electric vehicle transformer plates
POWER TORBEN
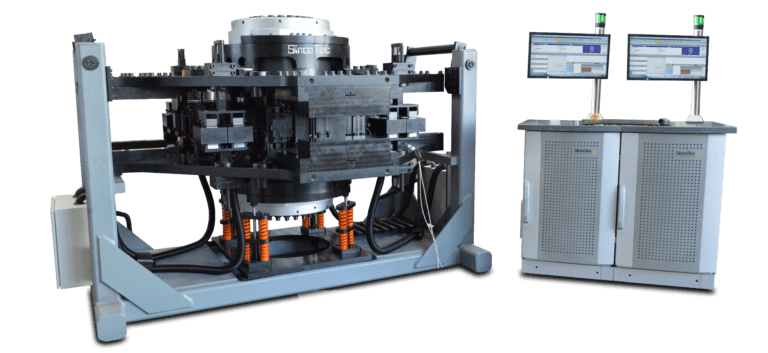

Torsion

Bending
Torsional bending test rig for crankshafts, shafts, and material samples for personal, commercial, and shipping
- 3 rig sizes for rated bending/torsion loads between 4,000/6,000 Nm and 200,000/300,000 Nm
- Application of combined and simultaneous bending and torsion loads
- Perfect tool to test the impact of multiaxial loads on the infinite fatigue strength of, for example, crankshafts
- Controlled phasing between bending and torsional loads
- Very low energy consumption <3 kWh
- Single load, bending or torsion, testing possible
- All the advantages of resonance test technology
Typical Components:
- Crankshaft offsets
- Shafts
- Material samples
The advanatages of resonance testing technology
The advanatages of resonance testing technology
- Highest energy efficiency = very small energy costs + short test times
- Automatic precision crack detection thanks to the resonance principle eliminating the need for optical crack detection
- Shorter test times for lifecycle testing
- High accuracy of target values leading to a scattering of real test results
- Tests costs are 1% of those when testing with servo-actuator-driven, also thanks to low maintenance and the use of low wear components
- Low operating costs thanks to the resonance principle and low infrastructure requirements
- Low noise profile
- Space efficient
- Proven test technology with over 1,500 test systems in use worldwide
